生産拠点の海外移転が進むなか、新たに再生ポリエステルの製造工場を立ち上げたベンチャー企業がある。繊維・プラスチックリサイクルの日本環境設計(東京)だ。昨年10月、北九州に年産2000トンの試験プラントを設け、このほど、企業買収で神奈川県川崎市に商業プラントを確保した。技術開発から生産、消費者参加型の回収インフラまで一貫するビジネスモデルで、繊維リサイクルの輪を国内外に広げる。
【関連記事】【素材イノベーター⑤】 あつまるホールディングス
仕組みから構築
「今でも建築の設計会社に間違えられます」と笑う髙尾正樹社長。社名に取り入れた〝設計〟は、学生時代に影響を受けた設計学からとった。教授が提唱した全体最適の考え方が、同社が目指す循環型社会の実現に欠かせないと考えたからだ。特に、サプライチェーンが長く複雑で、プレーヤーの多い繊維産業においては、「技術開発にとどまらず、消費者とのコミュニケーション、政策との整合性なども含む全体を設計する必要がある」と強調する。
創業は07年。繊維製品に多く使われている綿、ポリエステルに焦点を当て、繊維リサイクルの技術開発に取り組んだ。先行した綿は、衣料品に含まれる綿からエタノール燃料に生成する技術を確立。愛媛県今治市の工場で10年から本格生産を始め、染色工場などで使用されているほか、16年からは航空機の燃料に再生するプロジェクトも進む。
ポリエステルでは、衣料品からポリエステル繊維を分解、精製し、ポリエステル繊維の原料であるポリエステル樹脂に再生する技術を開発した。ポリエステルだけを解重合できるため、他の素材と組み合わせていたり、ボタンやファスナーが付いていたりしても、一般的な石油由来のポリエステルと同等の品質を持った原料が製造できる。
川崎に取得した商業プラントは現在、飲料用ペットボトルに特化しているが、20年をめどに衣料品でも再生ポリエステルを生産できるようにする。年間の生産能力は2万3000トン。北九州の試験プラントをマザー工場に、エネルギー効率の合理化、品質向上に力を入れ、高機能樹脂の開発にも取り組む。
主役は消費者
技術開発と並行して取り組んできたのが、消費者との接点作りだ。再生材にはコストダウンの課題が付きまとうが、「新しい売り方と付加価値で市場を作る」ことで、価格競争から一線を画す。
重く捉えられがちな環境活動を明るく、楽しく関われる仕組みに変えるのがその柱で、15年には回収衣料品から生成したバイオエタノールを燃料に、「デロリアン走らせるイベント」を開いた。コト消費の広がりもあり、消費者から古着を小売店の店頭で回収し、再生するブリングプロジェクト(旧FUKU-FUKUプロジェクト)は、参画企業が有力アパレルや小売店、セレクトショップなど約40社に広がっている。
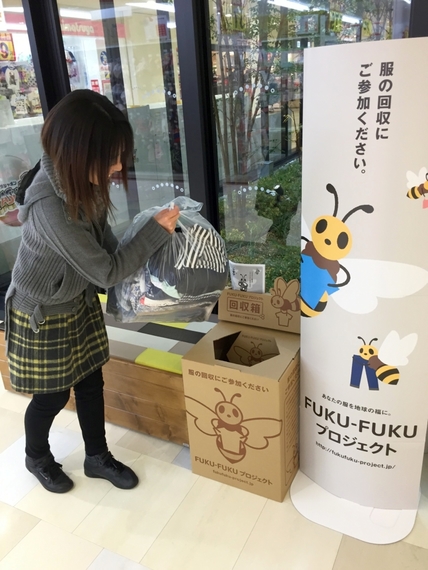
製造拠点を国内にこだわったのも、「消費者と気持ちを共有するには、距離が重要」だから。北九州の試験プラントは、消費者と共に衣料品の共同回収プロジェクトやワークショップを開催するコミュニティースペースとしても活用する。
「創業以来、リサイクルは必ず付加価値になると信じてきた」と髙尾社長。再生ポリエステルへの引き合いは、欧州のグローバルSPA(製造小売業)やアウトドア、スポーツアパレルなど海外が圧倒的だが、国内にも需要が拡大する兆しが出てきた。
回収量や再生ポリエステルの使用率など、具体的な目標値はあえて掲げていない。「本当に新しいことをしているので、状況は毎日のように変わる。その瞬間で、最も良い判断をしていく」ためだ。「まずは共に取り組む仲間を増やすことを大事にしたい」と髙尾社長。最近は、仏など海外からも同社のビジネスモデルに関心が向けられており、市場はグローバルに広がる。
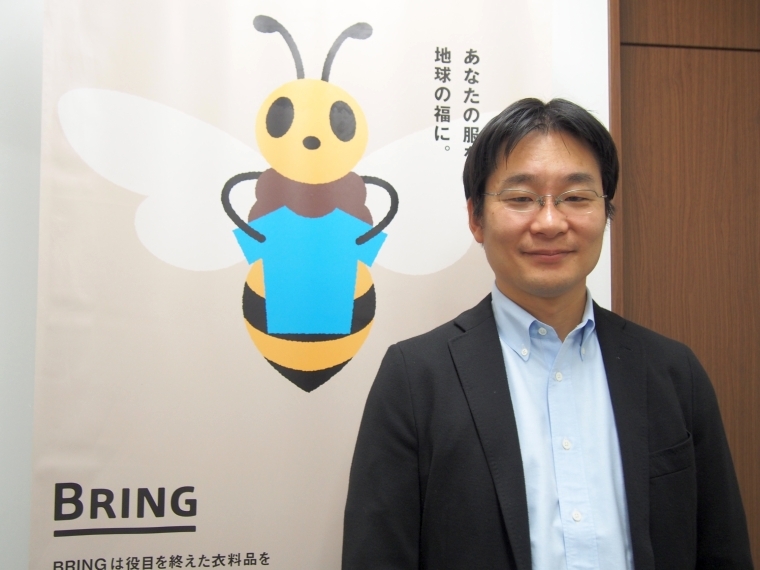